
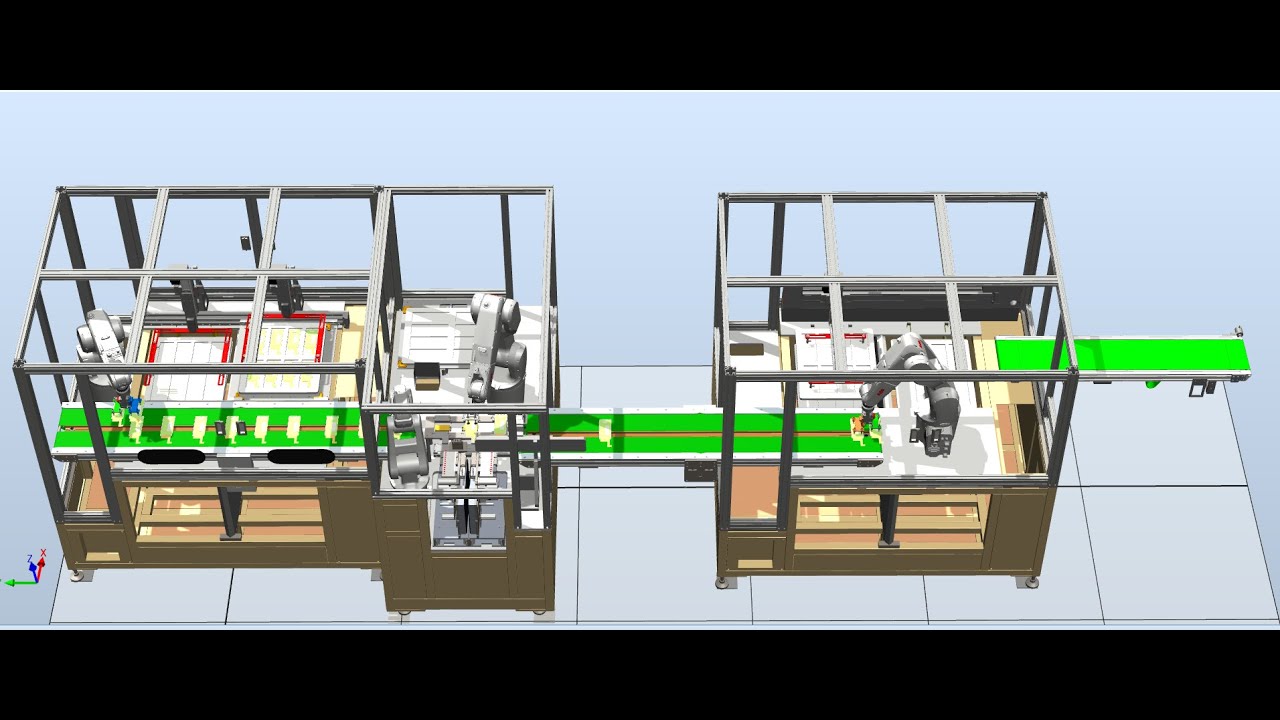
“The manufacturers of everything from mining vehicles to automobiles are using different materials to reduce cost and weight and to accommodate different powertrain solutions,” he said.
ROBOTSTUDIO SMART COMPONENT OFFLINE
Changing Materials Another Reason to Automate Offline programming makes it easier and faster to setup an automated welding process.Ĭhanges in work materials over the past ten years have driven improvements in welding, many of which are impossible to apply manually, such as laser welding, according to Erwin DiMalanta, director, welding & cutting business line, ABB Robotics(Auburn Hills, MI). “You still need a quality welding person to run that robot,” as Lange put it. But sources interviewed for this article stressed that it’s not a substitute for skilled labor. So robotic automation is a huge help in increasing throughput. If it’s two years, it’s something you should seriously consider.” Typically, if you can automate a process and get payback in less than year, that’s something you do right away. You’re saving two salaries per shift and the average pre-engineered cell cost is $100,000 to $120,000. “One robot system will make as many parts as three welders. Robotic welding helps fill that void.” Miller Electric and others offer pre-engineered robotic welding automation cells, including everything you need to weld except the power source and gas supply.Īt the same time, “the payback on a robotic system is typically much better than you might think,” explained Erik Miller, business development manager-laser group at Miller Electric Mfg. “But on any given day, the numbers of people retiring exceeds the incoming replacements, creating a void. “There are lots of tech schools throughout the country investing in welding programs to try to help bridge that gap,” Lange continued. It’s doubly important to make it easier on welders because they’re becoming harder to find.

Moving parts all day long and crawling under different fixtures is taxing on a human.

Number two is to reduce the abuse on the welder. But for most industrial applications and anything complex, robotic welding is ideal and is the focus of this article.Īs Jason Lange, manager inside sales, Lincoln Electric Co. (Cleveland) explained, “The main purpose of a robot is to help with the repeatability of a weld. For example, it’s generally the best solution for welding pipes. Fixed automation is often specific to the application and it’s best when the part geometry and the weld are very simple. There are two broad categories of automated welding, so-called “fixed” automation and “flexible” (or robotic) welding. Three Times Faster Even an automated welding system needs an experienced welder. Public class CodeBehind : SmartComponentCodeBehindĪBB. it the right time to automate your welding operation? Worried about how long you can keep your experienced welders? Need to increase your throughput but don’t see how with the available workforce? Challenged by tougher materials? A variety of technical advances make it relatively easy to solve these problems by automating your welding operation, with a surprisingly fast payback. The complete file is shown in the following snippet: using System Hello, my name is SmartComponent and I am being loaded! Running this component will produce the following output: Logger.AddMessage(new LogMessage("Hello, my name is " +Ĭ() + " and I am being loaded!")) public class CodeBehind : SmartComponentCodeBehind

We will access one if its properties (its name) and we will display it as a Public override void OnLoad(SmartComponent component)Īs mentioned before, the "component" argument contains the SmartComponent thatĬalled the function. Open the "CodeBehind.cs" source file of the SmartComponent and, inside the CodeBehind class, add the following overriding method: public class CodeBehind : SmartComponentCodeBehind
ROBOTSTUDIO SMART COMPONENT CODE
The code in this topic can be tested using the default RobotStudio Smart Component template.
